The European Agency for Safety and Health at Work (EU-OSHA) launched a Europe-wide campaign in 2018-2019 to risks from hazardous substances in workplaces in order to prevent
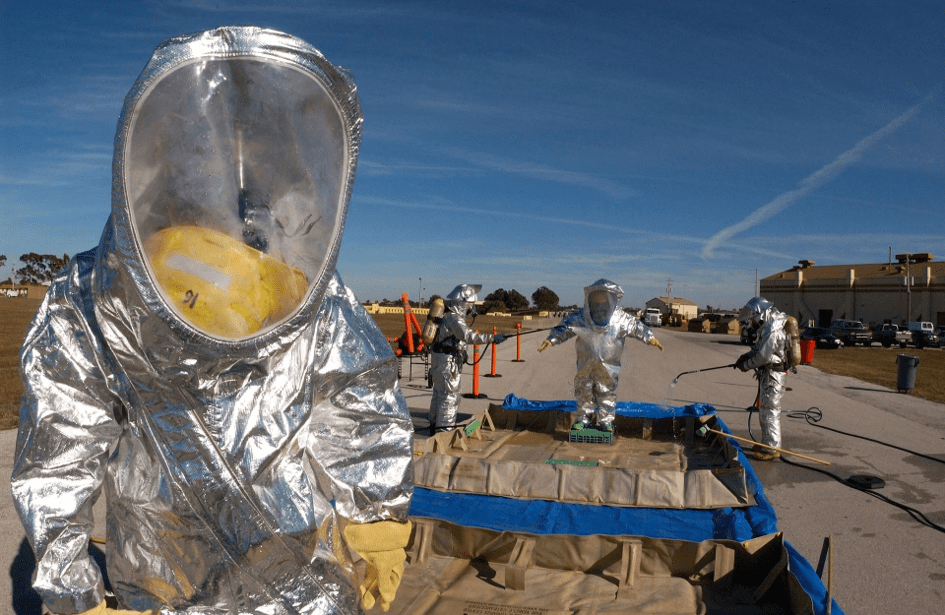
The aim of the campaign is to reduce exposure to hazardous substances in the workplace, by raising awareness of the risks and effective methods of their prevention.
Occupational exposure to hazardous substances continues to be a major safety and health problem, despite the fact that comprehensive EU legislation has been developed to control and reduce it.
The effects of contact with dangerous substances can range from temporary and mild health damage (e.g. skin irritation), to serious acute and chronic diseases (e.g. lung damage) and potentially fatal diseases (e.g. asbestosis and cancer). In addition, many hazardous materials are flammable or explosive, which poses additional safety risks. Furthermore, some materials, e.g. gases formed in waste water or leaking from cooling systems are acutely toxic or deadly.
In order to avoid and eliminate these effects, the employer must take the necessary measures. In order to reduce and avoid risks from exposure to hazardous substances, risk assessment is essential.
The European Union's Directive on Chemical Substances (CAD Directive) recommends following a hierarchy of control measures, i.e. "order of importance", in order to prevent or reduce contact with dangerous substances. At the top is full elimination, followed by the rest of the hierarchy:
- S = Substitution = the complete elimination of the hazardous substance or its replacement with a safer alternative
- T = Technological measures = minimizing the concentration of the hazardous substance in the contact zone
- O = Organizational, i.e. organizational measures = minimizing the number of workers exposed to the hazardous substance and/or the duration and intensity of the exposure
- P = Personal, i.e. personal protective equipment = protective clothing or protective equipment, e.g. wearing protective glasses and gloves as an exposure isolation device.
Identification of hazards and risks
This requires an inventory of dangerous substances. The inventory enables the comparison of material safety data and the prioritization of substances to be eliminated and replaced.
Safety and health protection data for chemicals can be found in the safety data sheets received from companies that distribute such products. In the case of substances generated during work processes (e.g. dust, combustion products) and naturally occurring substances (e.g. grain or flour dust, marble or heavy metals), the safety information - e.g. technical documents, handling and use instructions - can be obtained from product suppliers.
Material restrictions should be checked
The use of certain materials is subject to restrictions based on legislation and international or sector-specific agreements. Many materials cannot be used at all because they are banned. The use of others may be restricted by large organizations or conglomerates in the supply chain, such as in the electronics, automotive, and textile industries.
Conduct a comprehensive risk assessment
According to occupational health and safety legislation, a comprehensive risk assessment must be carried out. In the field of risks arising from hazardous substances, the dangers arising from the substances must be identified and explained, as well as the conditions of their use.
The risk assessment concerns the following:
- the number of workers exposed to hazardous substances;
- the level of exposure to workers;
- place of use – open or closed space;
- risk of skin contact;
- the risk of dispersion or spread in the air, for example, as a result of spraying.
Finding alternatives
Searching for materials that result in safer use. Information obtained from authorities, professional associations, trade unions, or even recommendations from suppliers can be of great help for this.
All alternatives must be evaluated using the same procedure. Hazard aspects must be examined and costs and benefits must be weighed.
Experimental study
The risks associated with unsuccessful substitution can be reduced by testing the given solution on a smaller, experimental scale. Consideration should be given to technological and organizational changes, especially the potential transformation of risks and control measures. The involvement of employees is essential in order to have a complete picture of the accompanying changes
Implementation and development
Full implementation of a substitute substance or process may require certain modifications to work procedures, materials or equipment. Employee feedback can be key to a successful replacement.
Introduction of a chemical management system
In order for substitution to become part of everyday work practice, a chemical management system that constantly questions the use of materials and prescribes substitution must be developed.
The summary was prepared on the basis of the European Agency for Safety and Health at Work, informational publication entitled "Substitution of hazardous substances in the workplace".
Source: http://www.ommf.gov.hu